Subscan Transforms Field Operations with BigChange Mobile Technology
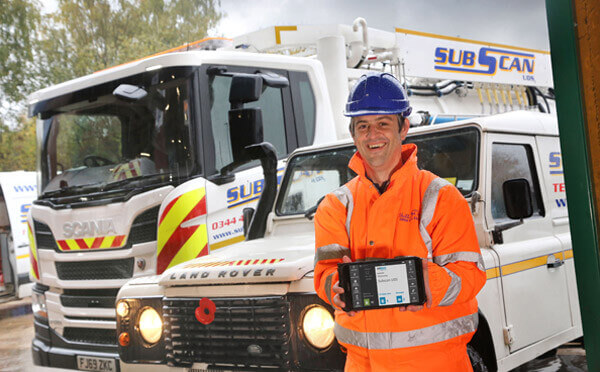
Subscan UDS, the nationwide utility, drainage, and survey company, has implemented a high tech mobile workforce system from Leeds technology company BigChange.
The system, which provides a paperless means of planning, managing, scheduling, and tracking mobile operations, has provided Subscan with a 30 percent saving in time and a million-pound growth boost to its business.
Subscan provides a wide range of services aimed at the detection and avoidance of underground utilities, as well as drainage maintenance and repairs. A team of specialist technicians operate across the UK undertaking everything from topographical surveys to underground utility tracing, drainage, CCTV surveying and the lining of drains.
Kirk Mason, Operations Director, Subscan says:
“We go and map areas identifying all structures and utilities above and below ground and then sort out any issues – we deal with all major infrastructure. We offer a full service package from initial survey to remedial work and when needed, new works including design and planning,”
Subscan has been a success story since formation only 7 years ago with steady year on year growth. However the previous IT system was proving to be a barrier to growth and with the move to BigChange the company has been able to expand and turnover is expected to increase from £6 million last year to £9 million in 2020.
Mason says:
“Our previous system only offered partial automation and we wasted a lot of time double touching to keep different systems up to date,”
“What we needed was a seamless flow of data from start to finish with an audit trail of activity. In the end there wasn’t anything that matched BigChange for functionality; it gives us that seamless connectivity and it has replaced 5 separate systems – saving us time and money.”
Subscan has equipped 50 of its field operatives with rugged tablets running JobWatch, the BigChange app for paperless working. Jobs are scheduled and sent to the assigned operative who can proceed straight to the job and with trackers on the fleet, the office has real time visibility of their locations.
Mason explains:
“With BigChange we are now very much paperless; it has been a complete digital transformation and the savings are significant. For time alone we are achieving savings of 30 percent and that’s before we even begin to look at the improved job scheduling and productivity,”
Subscan has a particularly strong commitment to quality and the company is ISO accredited for their management of quality, environmental, and health and safety.
Mason says:
“Our pursuit of quality drives the business – the quality of equipment, quality of people, quality of work and quality of service. BigChange is proving to be an invaluable tool in managing our ISO accreditations as the system ensures best practice procedures are followed at all times. Crucially it also provides an audit of activities and all the information we need to meet the required standards,”
he adds:
“One thing is very clear, since implementing BigChange we simply don’t get KPI failures as we are right on top of the workload and that’s meant we meet out SLA commitments and deliver a level of service we simply could not provide before,”
On site the JobWatch app takes operatives through workflow to ensure the correct procedures are followed and data is collected. The system ensures there is a complete record of every job which is including time and location referenced photographs; this is important for minimising invoice queries and also for supporting ISO accreditations.
Mason explains:
“BigChange has been crucial to allowing us to grow freely and being cloud-based we can add more operatives and services at the touch of a button and when we open up a new office down south next year, we’ll have a ready-made and instantly accessible IT solution already in place; its magic!”
BigChange vehicle tracking is not only useful for providing visibility to operations and customer services back in the office but it is also helping improve the quality of driving. Driver performance based on factors such as speed, braking, cornering and idling is graded automatically and those operatives with high ratings are rewarded with extra holiday vouchers.
Subscan has made a multi-million pound investment in the most advanced fleet of specialist vehicles in the UK. The 60 vehicle fleet includes JHL 312 and 414 recyclers and Mercedes Atego 204 Cityflex units. The JHL SuperRECycler 414, built on a Scania chassis, is the markets most powerful and productive recycling unit and both JHL models have fully automatic water filtration systems that continuously separate water from sludge to subsequently use the cleaned water to clean the sewer. Subscan has also invested in a JCB Fastrac 7230 tractor for rugged terrain operations.